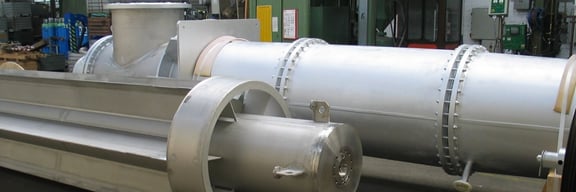
Caprolactam
More than 60 years thin film evaporation
Caprolactam
More than 60 years thin film evaporation
Industrial use of Caprolactam
In 2013 the invention of Nylon 6, also known under the brand name Perlon, had its 75th anniversary. Nylon 6 was developed by the German chemist Paul Schlack in order to get around an US patent for the production of Nylon 6,6, both very useful for the production of synthetic fibres. Nylon 6,6 is made from hexamethylenediamine and adipic acid, i. e. from two different molecules, while Nylon 6 or Perlon is produced from the Caprolactam molecule with the chemical formula C6H11NO only.
Early chemical processes for Caprolactam production needed complex distillation steps to clean the Caprolactam to a product quality which could be used for spinning. The Snia Viscosa “I-The process” used toluene as feedstock which had been converted in a series of process steps to Caprolactam. The raw Caprolactam solution was purified in a process stage with 6 Thin Film Evaporators /Sni 70/. “Unfortunately” state-of-the-art process designs usually do no longer need so many Thin Film Evaporators for Caprolactam purification.
Today Thin Film Evaporation is still used in the polymerisation of Caprolactam to Nylon 6. The polymerisation delivers a product which contains monomer and oligomers and other products from the polymerisation reaction. The monomers and the oligomers have to be extracted with water in order to avoid fibre breaking during spinning. Other processes, such as the depolymerisation of waste chips also produce water which contains Caprolactam. Due to the relatively high concentration and relatively high price of Caprolactam the recovery is an economical must for Nylon 6 producers.
The figure below shows a typical set-up of a Caprolactam recovery unit. The feed, a mixture of Caprolactam, oligomers and water, is pre-concentrated to about 70% Caprolactam. The remaining water is distilled under vacuum in Thin Film Evaporator 3. The residue is fed to Thin Film Evaporator 4. The bottom product of Thin Film Evaporator 4 consists of about 50% oligomers and 50% monomer. This product is crystallised and recycled to depolymerisation in order to use the expensive Caprocalctam as far as possible. The distillate of Thin Film Evaporator 3 is clean water, which can be re-used in the production process. The distillate of Thin Film Evaporator 4 is high quality Caprolactam which is recycled to the polymerisation, thus to the production of Nylon 6.
Sni 70: Snia Viscosa „Caprolactam from toluene“, someday in the 70ties
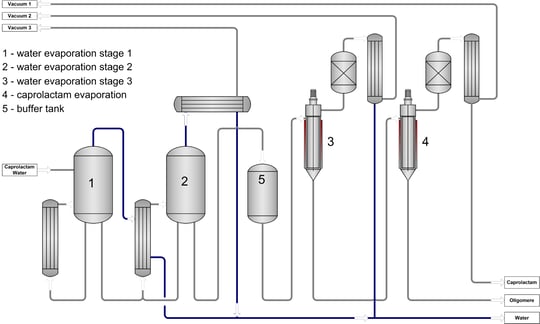