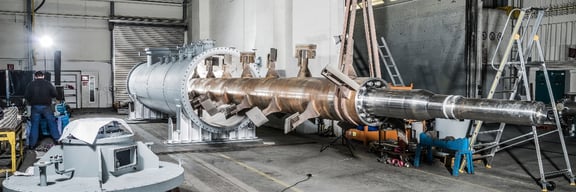
TDI
Recovery
TDI Recovery
TDI
Recovery
TDI Recovery
TDI - Precursor of polyurethane
A lot of daily life products are made from polymers based on toluene diisocyanate (TDI) like glue, soft foams for padding and mattresses, shoe soles, spray paintings for car industries, air crafts and trains. About 90 % of the world´s TDI production is used for polyurethane, a plastic which can be foamed and therefore is used in several high-volume applications.
Production process
The TDI production process yields substantial quantities of distillation residue which contain 30 to 70% by weight of free TDI. The recovery of this TDI is one of the process steps governing the overall economy of the TDI production process. Since the recovery is a difficult undertaking, several recovery methods have been developed:
- Chemical/physical separation using liquid-liquid-extraction
- Chemical transformation with conversion to Toluene diamine (TDA) and
- Thermal separation with evaporation and/or drying stage.
Thermal separation incl. drying stage allows a 100% recovery of the TDI from the residue and therefore is acknowledged as an up-to-date technology in TDI recovery.
TDI recovery
However, even though the recovery of 100% of TDI is theoretically possible, the realisation of the recovery process is very challenging. As soon as the free TDI content of the distillation residue decreases to about 17%, the concentrated residue becomes highly viscous, sticky and suddenly converts into a solid state. Therefore current process and equipment designs aim on avoiding the blocking by solid material. Convective dryers act as fluidised bed dryers under atmospheric pressure using nitrogen for fluidisation. The pre-concentrated residue is evenly distributed into the hot fluidised bed so that the conversion to the solid phase is very fast. Thus, the formation of the highly viscous intermediate phase is avoided and the distillation residue is quickly transformed into fine solid particles.
Contact dryers in TDI recovery use one or two agitators and are characterised by their large volume, their rugged, high torque and their double jacket design. Other characteristics are the containment of vapours and in some processes the use of additional high-boiling inert carbons to prevent caking of the solid residues on the agitator as well as on the walls. Usually contact dryers are operated under vacuum and in continuous operation.
Both implementations of the thermal separation TDI recovery process in convective and very special contact dryers have disadvantages resulting in high operation and/or investment costs. Therefore SMS developed a new process, the TDI recovery in a Combined Fluidisation Technology (CFT) dryer, which clearly improves the profitability of the TDI recovery process. Because of the working principle of CFT dryers, this type of dryer is the ideal equipment to simplify the TDI recovery process. The final dry residue is continuously discharged by gravity from the CFT dryer into a product cooler. The overall material balance proves 100% TDI recovery.
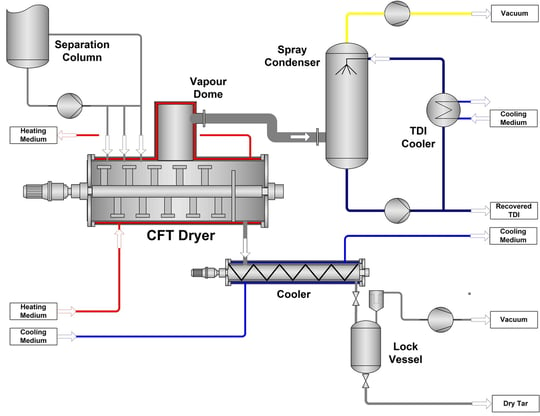
TDI recovery process with CFT

CFT for TDI recovery
Advantages
Based on our experience and our investigations in TDI recovery the new recovery process has the following main benefits:
- 100% TDI recovery
- Simple and continuous one step process
- Non-toxic and easy-to-handle dry product
- Clear improvement of process profitability
Residue granuales from TDI recovery