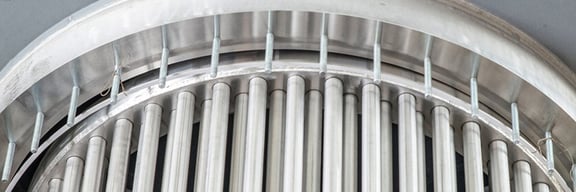
Short Path
Evaporator
Perfectly mastering thermal separation duties
Short Path
Evaporator
Perfectly mastering thermal separation duties
The perfect equipment for temperature-sensitive products
The SMS short path evaporators guarantee excellent results when evaporating, concentrating, distilling or devolatilising temperature-sensitive, high-boiling mixtures. The internal condenser minimises the pressure loss due to its short distance from the evaporation surface. Therefore, short path evaporators can operate under fine vacuum and with correspondingly low boiling temperatures. Even extremely heat-sensitive products, such as vitamins and flavourings, can be distilled without causing any thermal damage.
Advantages of SMS short path evaporators
- Very good vacuum up to 0.001 mbar (a) and low evaporation temperatures
- Short residence times and small amounts of product in the evaporator
- Newly invented and unmatched feed distribution system
- Unique droplet separation for outstanding distillate quality with lowest possible pressure loss
Working principle
Short path distillation is a thermal separation technology operating at process pressures in the range of 1 to 0,001 mbar. It lowers the boiling temperature and is an excellent method for gentle thermal treatment of heat-sensitive, high-boiling products. The short path evaporator consists basically of a cylindrical body with a heating jacket, a rotor and an internal condenser.
For the thermal separation of a mixture the rotor creates a mechanically agitated, thin product film on the heating surface inside the body. By means of gravity the product flows down in a spiral path whereby the volatile portion of the product evaporates. The vapour passes by the shortest route and with practically no pressure drops onto the internal condenser. The non-volatile portion as well as the vapour condensate reach the lower part of the evaporator and are discharged to separate bottom product outlets. The residual vapours and inert gases flow through the vacuum nozzle to the vacuum system.
In the gap between the rotor blade and the heating surface, fluid is supplied to the heat transfer surface with intense heat and mass transport. This results in a good heat transfer performance even with viscous products. In addition, the formation of deposits is avoided and the intensive mixing also protects temperature-sensitive products from overheating.
Another important task of the rotor is to stabilise the liquid film on the heating surface at high evaporation rates. This allows evaporation in the area of nucleate boiling without film rupture. At the same time the liquid film is pressed against the heating surface by the centrifugal force. This avoids the adverse evaporation mode in which a vapour layer with insulating effect is formed under the liquid film. Due to this operation principle extremely high specific evaporation rates are achievable.
Operating principle of short path distillation
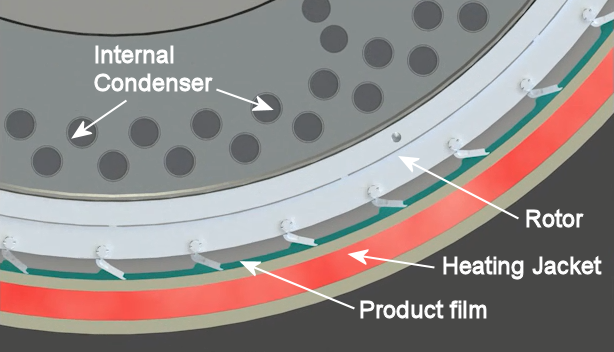
Design Features of Short Path Evaporators
SMS Short Path Evaporators are available in a unique variety of rotor designs comprising:
- PTFE or graphite wiper elements
- Spring-loaded PTFE or wiper elements
- Metal wiper elements
- Polymer or graphite rollers
- Hygienic design
The rotors can be equipped with specially designed splash guards, protecting the internal condenser from droplets in the vapour stream and ensuring highest distillate quality.
The internal condenser can be removed from the bottom of the short path evaporator. The majority of the short path evaporators is supplied with a tubular condenser, but SMS has designed special thermoplate condensers to meet the hygienic requirements of the food and pharmaceutical industry.
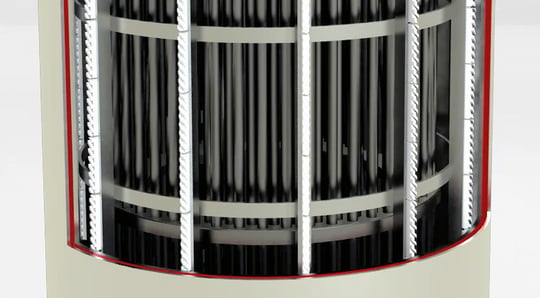
Rotor of short path evaporator with PTFE wiper elements
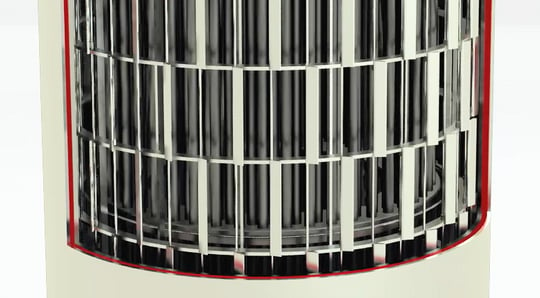
Rotor of short path evaporator with metal wipers
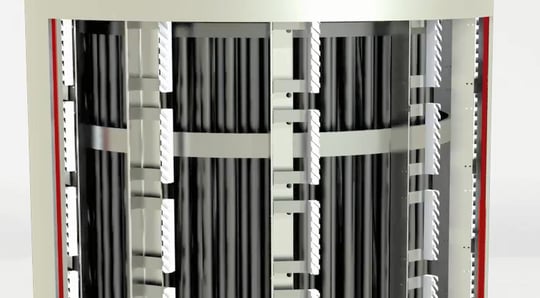
Rotor of short path evaporator with spring-loaded wipers
Typical Applications
The short path evaporator is specifically well suited for distillation, evaporation, concentration and stripping of heat-sensitive products such as:
- Monoglycerides
- Vitamins
- Silicone oils
- PTMEG
- Waxes
- Omega-3 fatty acids
- Waste oil
- Coal tar pitch