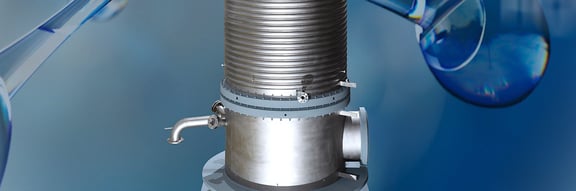
Chemical PET Recycling
with SMS Technology
The sustainable alternative to traditional recycling
Chemical PET Recycling
with SMS Technology
The sustainable alternative to traditional recycling
The future of sustainable plastics
As the global focus on sustainability intensifies, driven by growing environmental concerns and the urgent need to reduce carbon footprints, the plastics industry faces increasing pressure to find viable and effective alternatives to traditional recycling methods or to the use of crude oil as a primary raw material. This shift is not only a response to regulatory demands and consumer expectations but also a crucial step towards achieving a more sustainable and circular economy.
In this context, Buss-SMS-Canzler emerges as a pioneering leader, positioned at the forefront of this transformative shift with its innovative chemical PET recycling solutions. These solutions offer new perspectives and possibilities, enabling the industry to move beyond conventional practices and embrace more sustainable approaches that promise to significantly reduce environmental impact while maintaining the quality and functionality of plastic products.
Unlike traditional recycling methods that simply melt and filter PET (polyethylene terephthalate) to create a lower-quality recycled product, chemical recycling offers a more sophisticated and comprehensive approach by breaking down the polyester molecules into their original monomers.
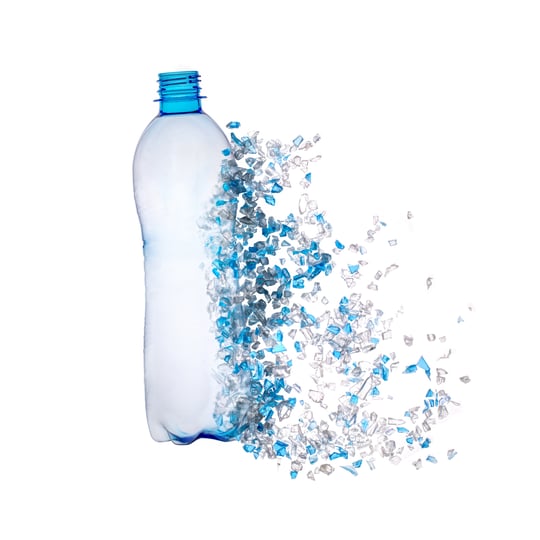
This advanced technique involves a series of complex processes such as:
- hydrolysis
- methanolysis
- glycolysis
- enzymolysis
Through these processes, essential monomers like terephthalic acid (TA) and ethylene glycol (EG) are recovered, along with pseudo-monomers such as BHET (bis(2-hydroxyethyl) terephthalate) or DMT (dimethyl terephthalate). These recovered components are then purified and can be re-polymerised to produce new virgin PET (vPET), effectively creating a closed-loop recycling solution.
This method not only ensures that the quality and integrity of the PET are maintained but also significantly reduces the environmental impact by minimising waste and conserving resources, thus contributing to a more sustainable and circular economy.
Purification processes
The most significant hurdle in the realm of chemical recycling is undoubtedly found within the purification processes that are integral to the functioning of depolymerisation reactors. This challenge arises due to the inherently complex nature of the mixtures of substances involved, which frequently display characteristics such as
- high viscosity
- severe crust formation
- abrasion
- reactivity
Conventional static systems quickly reach their operational limits. It is in these challenging circumstances that the innovative solutions developed by Buss-SMS-Canzler become crucial. The advanced technologies and specialised equipment are designed to address and overcome these specific issues, ensuring that the purification processes can proceed smoothly and effectively, even under the most demanding conditions.

SMS technologies and specialised equipment
Our specialised equipment, including advanced thin film evaporators, efficient short path evaporators, and high-performance thin film dryers, are meticulously engineered to tackle the most challenging and demanding stages of PET recycling. These sophisticated apparatuses are designed to ensure smooth, reliable, and uninterrupted operations across critical process steps, thereby enhancing the overall efficiency and effectiveness of the recycling process. By maintaining optimal performance, they contribute significantly to the quality and purity of the recycled materials, meeting the stringent standards required in the industry.
Over the past decade, SMS has diligently identified and encountered the following critical purification steps within the intricate process of chemical PET recycling, and it has adapted its machines ensuring that each piece of equipment is precisely engineered to effectively address these specific purification challenges:
- Drying of raw and purified terephthalic acid (CTA, PTA) after hydrolysis or enzymolysis (or BHET)
- Evaporation of ethylene glycol (EG) and diethylene glycol (DEG) from glycolysates and hydrolysates
- Evaporation of BHET (bishydroxyethyl terephthalate) from pre-concentrated glycolysates
Tailored solutions for maximum efficiency
Depending on the PET source and the specific process requirements, the properties of the monomers can vary significantly, presenting unique challenges and opportunities in the recycling process. To address these variations and ensure optimal performance, SMS offers its state-of-the-art test centre with laboratories and pilot plants located in Switzerland. These facilities are equipped with advanced technology and staffed by experienced professionals who work diligently to adapt the machines to the specific properties of the monomers being processed.
By providing tailor-made solutions, manufacturers are empowered to optimise the chemical recycling process, which not only enhances the efficiency of the operation but also significantly improves the purity and quality of the final product.
Our highly adaptable systems are designed to guarantee maximum reliability and performance, regardless of the process type employed. This commitment to customisation and innovation supports our dedication to sustainable and future-oriented recycling practices.
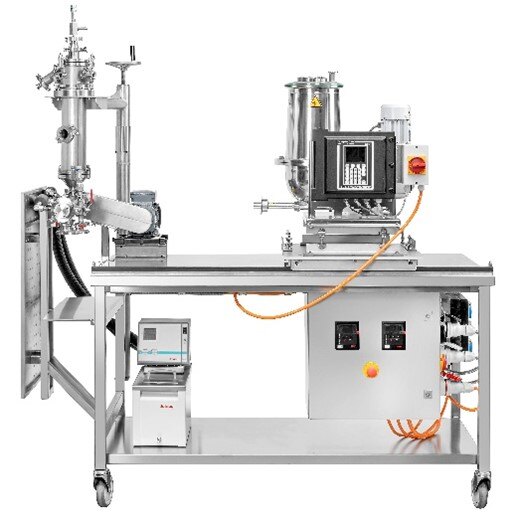
Consult our PET recycling expert
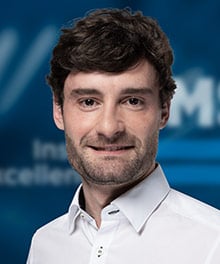
Tim Holtkamp
Tel. +41 61 8256 206
"Buss-SMS-Canzler is committed to advancing chemical PET recycling with innovative purification technologies. Our tailored solutions ensure efficient monomer recovery, supporting a true circular economy. By optimising processes, we help manufacturers overcome challenges and drive sustainable, future-oriented recycling."